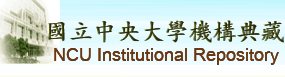 |
English
|
正體中文
|
简体中文
|
全文筆數/總筆數 : 80990/80990 (100%)
造訪人次 : 41634441
線上人數 : 2643
|
|
|
資料載入中.....
|
請使用永久網址來引用或連結此文件:
http://ir.lib.ncu.edu.tw/handle/987654321/2487
|
題名: | 鋁合金熱合氧化膜與陽極氧化膜成長行為之研究;Thermally-Formed and Anodic Aluminum Oxide Growth Behavior |
作者: | 魏百盛;Pai-Sheng Wei |
貢獻者: | 機械工程研究所 |
關鍵詞: | 陽極處理;鋁合金;Aluminum;Nanostructure;Anodizing |
日期: | 2007-10-12 |
上傳時間: | 2009-09-21 11:48:16 (UTC+8) |
出版者: | 國立中央大學圖書館 |
摘要: | 本研究主要在觀察鋁合金在不同條件下的氧化行為。研究方向分為三個部分:第一部份為觀察純鋁在高溫環境的氧化行為,瞭解空氣中氧化皮膜生長的情形,並觀察空孔與氣泡於熔溶鋁中的生成與成長模式;第二部份為鋁合金的陽極氧化行為之觀察;第三部份為陽極皮膜光學性質的研究。以下針對各主題加以說明: 第一部份:實驗所使用的材料為純鋁(99.999 %)與鋁-矽合金(Al-7 w.t.% Si)。首先,利用砂紙研磨除去試片表面因自然氧化而產生的氧化鋁,將純鋁試片放置於空氣爐中,加熱至873K並持溫25小時,利用SEM、TGA與低掠角XRD等儀器,紀錄高溫下鋁的氧化皮膜生長歷程與觀察微結晶結構的變化。 第二部份:主要是,觀察鋁合金陽極皮膜生長情形。記錄純鋁與商用Al1050合金在不同陽極條件的電壓與時間圖;將電壓與時間圖作一次微分,配合皮膜結構的觀察,觀察陽極皮膜的生長過程,由實驗結果得知,皮膜生長依序可以分為四個階段---緻密層生長、微孔成核(pore initiate)、孔洞擴展(pore widening)與皮膜穩定成長(quasi-steady state)階段。陽極處理時,由電壓-時間的微分曲線圖形變化,可以判斷pitting 是否出現,藉此可決定較適合的陽極處理條件。接著,比較純鋁與商用Al1050合金的陽極行為差異,使用SEM與TEM觀察Al1050合金內部雜質在陽極過程中的行為。由電子顯微鏡的觀察可知雜質原子是由Al-Si-Fe三元素所構成;由電壓與時間關係圖可知,Al-Si-Fe顆粒狀雜質的存在會降低陽極電壓,主要是因為Al-Si-Fe的顆粒狀雜質會參與反應,經過陽極處理,顆粒狀雜質會變成多孔型態。 第三部份:使用的材料為商用Al1050與Al5052滾軋鈑。試片經過陽極處理後,利用色差計檢視試片表面對光反射的光學性質。利用SEM檢測試片表面奈米孔洞的尺寸與分佈,探討反射率與試片奈米結構的關係。比較不同的基材(Al1050與Al5052)陽極表面的顏色差異。 This thesis aimed at investigating alumina oxide film formed on aluminum, which is the most popular light metal applying to many common purposes. The study can be divided into three main parts. First, the observation of thermally-formed aluminum oxide on pure aluminum was conducted. The formation of pores and microbubbles derived by hydrogen in aluminum was brought out. Second, the anodic oxide films formed on aluminum were observed. In the part of this study, we measured and recorded the potential and processing time during anodizing treatment performed in different substrate. There are some critical points on the differentiated curves (ΔV/Δt) obtained from the measured data which most likely correspond to micropore initiation and pitting formation. Some more subjects about anodic oxide film were presented. Third, Optical properties of anodic aluminum oxide films on Al1050 and Al5052 alloys were investigated. The individual briefs are as following: PartⅠ: Pure aluminum (99.999%) cubes were polished by abrasive papers then heated in furnace at 873K for 25 hr to grow oxide on the polished surfaces and coded as Al/oxide. The thermally-formed oxide was investigated with SEM and G.I.A in order to reveal the structure of oxide. These Al/oxide samples were stacked with pure Al cube and Al-7mass%Si cube respectively then heated in furnace at 1023K for 1200 s in an Ar+H2 atmospheric gas. The sandwich samples were sectioned and polished after the heated sample cooled to room temperature. The morphologies of interface (or junction of the sandwich samples) were recorded photographically. Based on the recorded cavities shown at the interface, we measured both the radii of curvatures and contact angles of cavities. When the Al/oxide stacking with pure Al sandwich samples heated in Ar plus H2 gas, cavities were readily shown at the interface; very few cavities has been observed when samples heated in Ar gas. Air-pocket initiated at the microchannels by hydrogen diffusion then grew and coalesced at the interface. The air-pockets remained at the interface of heated Al/oxide stacking with pure Al sandwich sample and entrapped as cavities after samples solidified. Microbubbles detached from the airpocket forming micropores trapped in matrix of the Al/oxide stacking with Al-7mass% Si cube sample. PartⅡ: The formation behavior of anodic oxide film formed on aluminum was observed. In this part the relation of the anodic potential versus processing time was recorded for the anodizing of an Al1050 aluminum sheet in a sulfuric acid solution. The electrochemical behavior of aluminum during the anodizing treatment can be characterized by measuring the anodic potential-time curves. The nanostructure of anodic films was observed with transmission electron microscopy (TEM) and high resolution Field-Emission Scanning electron microscopy (SEM). The differentiated curves (ΔV/Δt) could be partitioned into four steps indicating the processing conditions during the growth of the anodic film: barrier layer formation, nanopore initiation and growth, pore widening, and quasi-steady state growth of the anodic film. Pitting during the pore widening stage could be characterized by looking at the different types of valleys in the differentiated curve. The effects of the anodic parameters, such as the acid concentration, bath temperature, current density and impurities, on pitting formation were investigated and some conclusions offered. PartⅢ: A spectrophotometer was used to measure the surface reflectance of AAO films, which formed from the different processing conditions on Al1050 and Al5052 alloys. The factors that affected the reflectance of AAO film were discussed. After cleaning and desmutting Al1050 and Al5052 alloys sheets were anodized in a 15% w/w sulfuric acid solution at 1.2-1.8 A*dm-2 and 283~303K. The potential-time curves were recorded during the anodizing process. The nano-structure of the AAO films changed with the anodic current density and the bath temperature. The area fraction of nano-pores on the anodic film increased with increasing bath temperature and with decreasing anodic current density. A spectrophotometer was used to measure the surface reflectance of AAO films, which formed from the different processing conditions. The factors that affected the reflectance of AAO films are discussed. |
顯示於類別: | [機械工程研究所] 博碩士論文
|
在NCUIR中所有的資料項目都受到原著作權保護.
|
::: Copyright National Central University. | 國立中央大學圖書館版權所有 | 收藏本站 | 設為首頁 | 最佳瀏覽畫面: 1024*768 | 建站日期:8-24-2009 :::