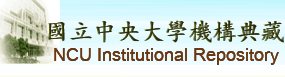 |
English
|
正體中文
|
简体中文
|
全文筆數/總筆數 : 82005/82005 (100%)
造訪人次 : 53310832
線上人數 : 1417
|
|
|
資料載入中.....
|
請使用永久網址來引用或連結此文件:
https://ir.lib.ncu.edu.tw/handle/987654321/93880
|
題名: | 製造圓柱型蝸桿之動力刮削刀具設計;Design of Power Skiving Cutter for Manufacturing Cylindrical Worms |
作者: | 林潔炘;Lin, Chien-Hsin |
貢獻者: | 機械工程學系 |
關鍵詞: | 圓柱型蝸桿;NURBS;最佳化;動力刮削刀具;有效重磨量 |
日期: | 2023-11-29 |
上傳時間: | 2024-09-19 17:44:13 (UTC+8) |
出版者: | 國立中央大學 |
摘要: | 傳統蝸桿製造通常使用車刀和磨輪加工,如今隨著動力刮削技術的發展,除了切削 常見的內齒輪外,小模數之蝸桿也可以用動力刮削加工。本論文首先運用齒輪原理及微 分幾何,模擬切削 ZA 型、ZN 型、ZI 型、ZK 型、ZC 型蝸桿,推導出此五型蝸桿之齒面數學模式。分別將五型蝸桿之齒面數學模式,藉由動力刮削之切削運動關係及嚙合方程式,建立動力刮削刀具前刀面之刃口線數學模式,再透過磨輪研磨刀具之運動關係,推導得到磨削此刀具之磨輪設計。 為了驗證本研究求得之磨輪與刀具設計過程,首先利用最佳化程式,以NURBS曲線針對磨輪進行擬合,並確認擬合準確度。接著將擬合之磨輪輪廓,推導至動力刮削刀具之設計前刀面,並以此刀具切削五型蝸桿。計算以動力刮削刀具切削之蝸桿與理論蝸桿間之齒形誤差,驗證刀具輪廓之正確性。 對刀具進行重磨可有效延長刀具壽命,故探討動力刮削刀具重磨量變化,對蝸桿齒形誤差與精度的影響,以DIN 7級作為目標,分別計算動力刮削刀具切削之五型蝸桿齒形誤差及精度,分析不同重磨量對精度之影響。為了確認動力刮削刀具之適用範圍,使用刀具切削不同參數之五型蝸桿,計算其誤差及精度,並探討其有效重磨量之變化。;Traditional worm manufacturing typically involves using turning and grinding processes. However, with the advancement of power skiving technology, it is now possible to use power skiving for the production of small module worms in addition to the internal gears. This paper begins by utilizing gear theory and differential geometry to simulate the cutting motion of five different types of worms, namely ZA-type, ZN-type, ZI-type, ZK-type, and ZC-type, and derives mathematical models of five types of worms. Using these mathematical models of five types of worms along with the cutting motion relationships in power skiving and equation of meshing, mathematical models of the edge profiles of the power skiving tools are established. Furthermore, the grinding wheels design for grinding these cutters are derived through the motion relationships involved in grinding the cutters. To validate the grinding wheels and cutters design process in this study, an optimization program is first employed to fit NURBS curves to the grinding wheel and confirm the accuracy of the fit. Subsequently, the fitted grinding wheel profile is transferred to the design of the edge profile of the power skiving tool, which is then used to cut the five types of worms. The tooth profile error between the worms cut with the designed tools and the theoretical worms is calculated to verify the correctness of the tool profile. Regrinding the tools can effectively extend their lifespan. Therefore, the study explores the impact of changes in the amount of regrinding on the tooth profile error and accuracy of the worms, with DIN 7 class as the target accuracy level. The tooth profile error and accuracy of the five types of worms cut with the designed tools are calculated for different amounts of regrinding to analyze the effect on accuracy. To determine the applicability of the designed tools, different parameters for the five types of worms are cut using these tools, and their errors and accuracy are calculated. The variations in the effective regrinding amount are also investigated. |
顯示於類別: | [機械工程研究所] 博碩士論文
|
文件中的檔案:
檔案 |
描述 |
大小 | 格式 | 瀏覽次數 |
index.html | | 0Kb | HTML | 87 | 檢視/開啟 |
|
在NCUIR中所有的資料項目都受到原著作權保護.
|
::: Copyright National Central University. | 國立中央大學圖書館版權所有 | 收藏本站 | 設為首頁 | 最佳瀏覽畫面: 1024*768 | 建站日期:8-24-2009 :::